Opening the Power of Welding WPS: Techniques for Effectiveness and Safety And Security in Fabrication
In the world of manufacture, Welding Procedure Requirements (WPS) stand as the foundation of welding operations, determining the needed actions for attaining both performance and safety in the fabrication procedure. Comprehending the intricacies of WPS is vital to harnessing its complete possibility, yet many companies battle to unlock the real power that lies within these records (welding WPS). By diving into the techniques that optimize welding WPS, a world of enhanced efficiency and increased safety waits for those ready to explore the subtleties of this crucial aspect of manufacture

Importance of Welding WPS
The importance of Welding Procedure Specifications (WPS) in the fabrication industry can not be overemphasized. WPS serve as a vital roadmap that lays out the necessary actions to make sure welds are carried out regularly and appropriately. By specifying crucial parameters such as welding processes, materials, joint styles, preheat temperatures, interpass temperatures, filler metals, and post-weld warm treatment needs, WPS provide a standardized technique to welding that improves effectiveness, top quality, and safety and security in construction processes.
Adherence to WPS assists in achieving uniformity in weld quality, decreasing the probability of flaws or structural failures. This standardization likewise assists in conformity with market laws and codes, making sure that fabricated structures fulfill the called for safety and security standards. In addition, WPS documentation allows welders to reproduce effective welding procedures, leading to consistent results across different tasks.
In significance, the meticulous growth and stringent adherence to Welding Procedure Specs are vital for maintaining the stability of bonded frameworks, guarding against potential threats, and maintaining the reputation of fabrication firms for supplying top quality product or services.
Secret Aspects of Welding WPS

Enhancing Efficiency With WPS
When enhancing welding procedures, leveraging the crucial components outlined in Welding Procedure Requirements (WPS) comes to be important for making best use of and improving procedures performance. One way to improve efficiency with WPS is by thoroughly picking the ideal welding specifications.
In addition, proper training and qualification of welders in understanding and implementing WPS can even more boost efficiency. Ensuring that all employee are fluent in interpreting and executing the WPS properly can minimize mistakes and revamp, conserving both time and sources. Regularly assessing and upgrading the WPS to include any kind of lessons found out or technical innovations can additionally add to effectiveness improvements in welding procedures. By welcoming the guidelines stated in the WPS and continually seeking ways to enhance procedures, makers can achieve higher efficiency levels and remarkable end outcomes.
Ensuring Safety in Construction
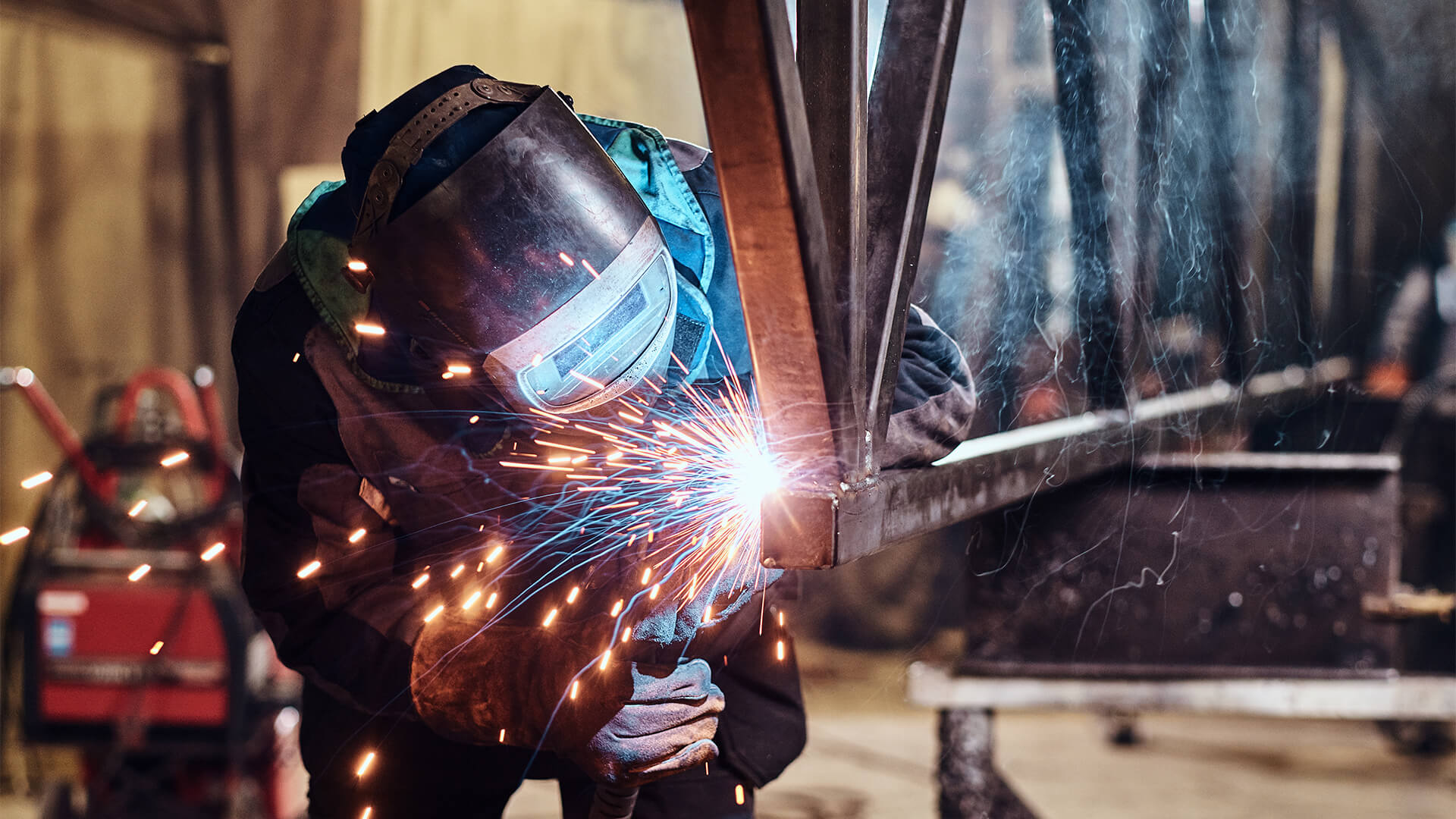
Ensuring safety in fabrication involves a complex method that incorporates various elements of the welding procedure. Welders need to be equipped with appropriate gear such as headgears, gloves, and protective clothing to minimize threats associated with welding activities.
In addition, adherence to appropriate air flow and fume extraction systems is critical in preserving a healthy job setting. Welding fumes have harmful compounds that, if breathed in, can position severe wellness dangers. Applying reliable air flow steps aids to minimize direct exposure to these harmful fumes, advertising respiratory system health and wellness amongst workers.
Regular equipment upkeep and inspections are likewise vital for making certain safety and security in construction. Malfunctioning equipment can cause mishaps and injuries, underscoring the additional resources value of timely repair work and routine checks. By focusing on precaution and fostering a society of awareness, manufacture centers can create a productive and safe and secure work setting for their workers.
Implementing WPS Finest Practices
To improve functional efficiency and guarantee high quality end results in fabrication procedures, including Welding Treatment Spec (WPS) ideal methods is paramount. Selecting the ideal welding process, filler product, and preheat temperature level specified in the WPS is important for accomplishing the desired weld high quality. Ensuring that certified welders with the essential certifications bring out the welding procedures according to the WPS standards is crucial for consistency and dependability.
Verdict
In verdict, welding WPS plays a critical function in guaranteeing efficiency and safety in manufacture procedures. By following these strategies, organizations can unlock you could look here the complete potential of welding WPS in their construction operations.
In the world of fabrication, Welding Treatment Specs (WPS) stand as click here to read the backbone of welding operations, determining the required actions for achieving both effectiveness and safety in the manufacture process. By defining essential specifications such as welding procedures, products, joint layouts, preheat temperature levels, interpass temperature levels, filler steels, and post-weld warmth treatment demands, WPS offer a standard method to welding that improves efficiency, quality, and security in manufacture processes.
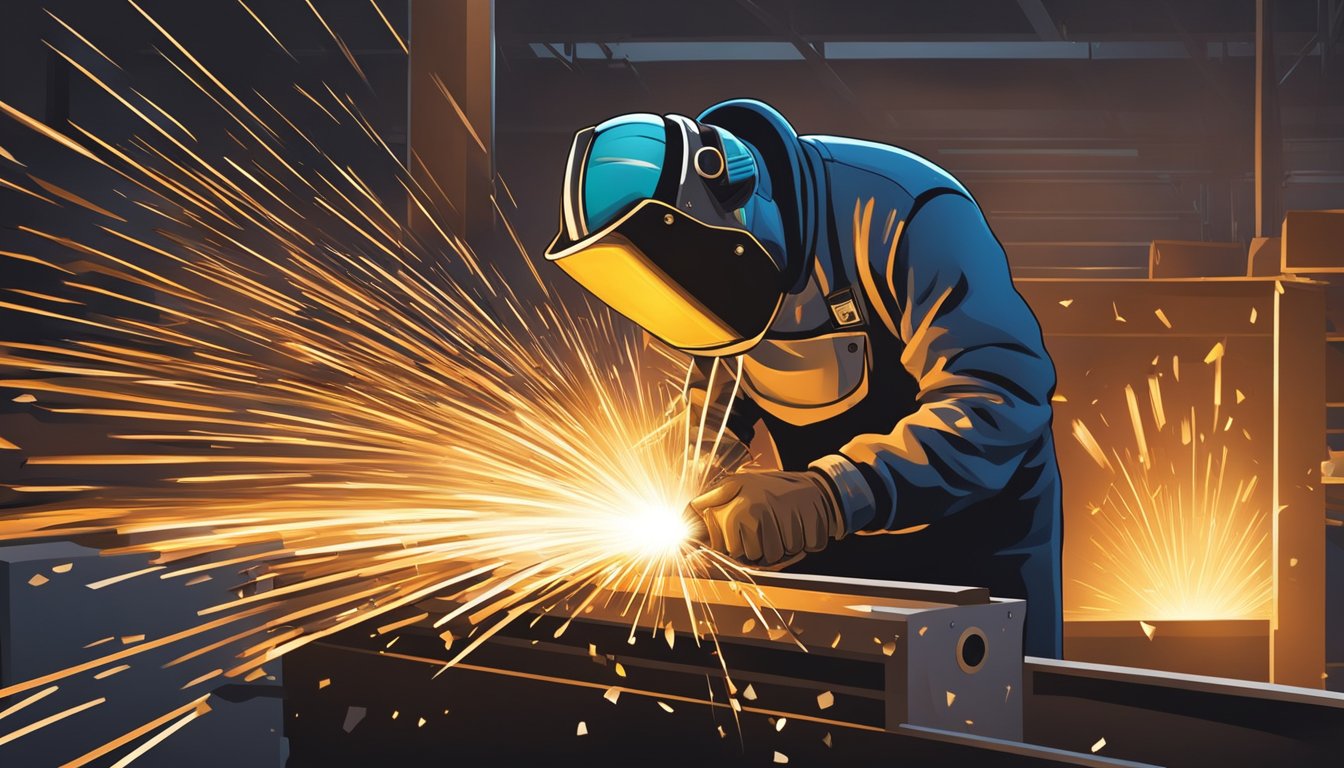
When maximizing welding procedures, leveraging the key elements outlined in Welding Treatment Requirements (WPS) becomes necessary for taking full advantage of and enhancing processes productivity. (welding WPS)